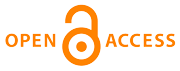 |
Home
>
Journal Issues
>
No 2 (2019) Technical mechanics
>
9
___________________________________________________
UDC 539.376
Technical mechanics, 2019, 2, 93 - 101
PREDICTION OF STRUCTURAL MATERIAL LIFE IN ISOTHERMAL CREEP UNDER COMBINED STRESS CONDITIONS
DOI:
https://doi.org/10.15407/itm2019.02.093
Doyar I. A., Poshyvalov V. P.
Doyar I. A.
Institute of Technical Mechanics
of the National Academy of Sciences of Ukraine and the State Space Agency of Ukraine
Poshyvalov V. P.
Institute of Technical Mechanics
of the National Academy of Sciences of Ukraine and the State Space Agency of Ukraine
This paper proposes a method for the prediction of structural material life in isothermal creep under combined
stress conditions verified using experimental data on the durability of tubular specimens of EI437BU-VD
heat-resistant nickel alloy at 650 ?C under the simultaneous action of an axial and a tangential stress.
A power, an exponential, and a fractional power dependence of the time to failure on the equivalent stress
were adopted as parametric durability models. Four expressions for the equivalent stress were considered.
Based on experimental data on the durability of tubular specimens of EI437BU-VD heat-resistant nickel alloy
at 650 ?C, the constants appearing in the expressions for the durability were estimated for each of the four
expressions for the equivalent stress using the least squares method.
For each parametric durability model, two types of prediction error were calculated. It was shown that for each
model the errors are minimized if the Mises criterion is taken as the equivalent stress.
For the exponential durability model and the Mises equivalent stress, the normal distribution hypothesis
for the random durability was tested using the values of its sample vector. Because of the small amount
of experimental data, the Shapiro–Wilk statistical criterion was used in the test.
The paper presents graphs of the distribution function and distribution density of the time to failure
for tubular specimens of EI437BU-VD heat-resistant nickel alloy at an axial stress of 490.5 MPa, a tangential
stress of 245 MPA, and a temperature of 650 °Ñ and the predicted specified life for different values
of the load parameters at a fixed confidence probability. At a confidence probability of 0.99, all
the experimental values of the time to failure lie on the right of the specified life, as distinct
from the values that correspond to a confidence probability of 0.9 and 0.95.
A technique for material creep constant identification is proposed. The technique is based on statistical
treatment of experimental creep curves and uses probability theory, mathematical statistics, and
optimization methods.
durability, lifetime models, creep constants, time to failure, equivalent stress, prediction errors
1. Lokoshchenko A. M. Simulation of Metal Creep and Durability. Moscow: Moscow State Industrial University, 2007. 264 pp. (in Russian).
2. Johnson A.E. Complex-stress creep of metals. Metallurgical Reviews. 1960. V. 5. No. 20. Pp. 447-506.
https://doi.org/10.1179/mtlr.1960.5.1.447
3. Lokoshchenko A. M., Shesterikov S. A. Creep. Summary of Science. Ser. Mechanics. Moscow: All-Union Institute for Scientific and Technical Information, 1965. Pp. 177-227. (in Russian).
4. Shesterikov S. A., Lokoshchenko A. M. Metal creep and durability. Summary of Science and Technology. Ser. Deformable Solid Mechanics. Moscow: All-Union Institute for Scientific and Technical Information, 1980. V. 13. Pp. 3-104. (in Russian).
5. Browne R. J., Lonsdale D., Flewitt P. E. J. Multiaxial stress rupture testing and compendium of data for creep resisting steels. Trans. ASME. J. Eng. Mater. Tech. 1982. V. 104. No. 4. Pp. 291-296.
https://doi.org/10.1115/1.3225079
6. Pisarenko G. S., Lebedev A. A. Material Deformation and Strength Under Combined Stress Conditions. Kyiv: Naukova Dumka, 1976. 415 pp. (in Russian).
7. Lebedev A. A. (Ed.), Kovalchuk B. I., Giginyak F. F., Lamashensky V. P. Mechanical Properties of Structural materials Under Combined Stress Conditions. Kyiv: In Yure Publishing House, 2003. 540 pp. (in Russian).
8. Golubovsky E. P., Demidov A. G. Durability assessment for EI437 BU-VD alloy for gas-turbine engine discs under combined stress conditions. Vestnik Dvigatelestroyeniya. Zaporizhzhya: Motor-Sich, 2008. Pp. 106-110. (in Russian).
9. Lokoshchenko A. M., Nazarov V. V., Platonov D. O., Shesterikov S. A. Analysis of long-term strength criteria for metals under complex stress state. Mech. Solids. 2003. V. 38. No. 2. Pp. 113-121.
10. Lokoshchenko A. M. Equivalent stresses in calculations of metal durability under combined stress conditions (review). Izvestiya Saratovskogo Universiteta. Ser. Matematika. Mekhanika. Informatika. 2009. V. 9. Iss. 4. Part 2. Pp. 128-135. (in Russian).
11. Lokoshchenko A. M. Criteria for determining the long-term strength under conditions of complex loading. Strength of Materials. 1989. V. 21. No. 9. Pp. 1121-1124.
https://doi.org/10.1007/BF01529282
12. Doyar I., Poshyvalov V. Development of a stochastic model of failure of structural materials in creep at hardening stage (in Russian). Eastern-European Journal of Enterprise Technologies. 2016. V.3. No. 5(81). Pp. 25-31.
https://doi.org/10.15587/1729-4061.2016.69653
13. Shiryaev A. N. Probability. Moscow: Nauka, 1989. 640 pp. (in Russian).
DOI:
https://doi.org/10.15407/itm2019.02.093
Copyright (©) 2019 Doyar I. A., Poshyvalov V. P.
Copyright © 2014-2019 Technical mechanics
____________________________________________________________________________________________________________________________
|
GUIDE FOR AUTHORS
====================
Open Access Policy
====================
REGULATIONS
on the ethics of publications
====================
|