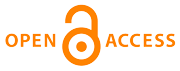 |
Home
>
Journal Issues
>
¹ 2 (2018) Technical mechanics
>
10
___________________________________________________
UDC 622.73
Technical mechanics, 2018, 2, 113 - 123
DEVELOPMENT OF A MODEL SYSTEM FOR CONTROLLING THE JET GRINDING PLANT OPERATION
DOI:
https://doi.org/10.15407/itm2018.02.113
Pryadko N. S., Strelnykov G. A., Muzyka L. V.
Pryadko N. S.
Institute of Technical Mechanics of the National Academy of Sciences of Ukraine and the State Space Agency of Ukraine
Ukraine
Strelnykov G. A.
Institute of Technical Mechanics of the National Academy of Sciences of Ukraine and the State Space Agency of Ukraine
Ukraine
Muzyka L. V.
Institute of Technical Mechanics of the National Academy of Sciences of Ukraine and the State Space Agency of Ukraine
Ukraine
Because of the increasing demand for fine-dispersed products in many industries, on the hand,
and the high energy intensity of the grinding process, on the other hand, the problem of fine
grinder productivity improvement and power consumption reduction is quite topical. The aim of
this paper is to develop a system for monitoring and controlling the productivity of a jet
grinding plant based on the results of acoustic monitoring of its working areas. The new
approach consists in continuously monitoring the material grain-size composition and forming
control actions on the circulating load of the grinding plant based on the analysis of the
acoustic signals analysis from the grinding chamber.
The main factors that affect the efficiency of closed-loop jet grinding were studied, and a
three-level model of the grinding process was constructed. The model accounts for the features
of grinding loop, the kinetics of the material grain-size composition in the grinding chamber,
and the relation between the grinding process and the acoustic signal characteristics. It was
shown that increasing the yield of a finished product of a given size calls for monitoring
the acoustic signals of the grinding zone and controlling the grinding chamber loading in
accordance with them in order to maintain it at the optimum level. This study may be a basis
for the development of an auto-mated control system for a jet grinding plant. Installing such
a system in the finished transportation zone down-stream of a granulometer-type classifier
would allow one to introduce an additional correction making the quality monitoring nearly
continuous. From the characteristics of the recorded acoustic signals, the system automatically
detects the presence of particles larger than the reference in the two-phase flow and points
to the need for adjust-ing the classification regime. The elimination of the re-grinding
probability improves the product quality and reduces the power consumption. These studies
will be a basis for refining the model of an automated control system for a jet grinding
plant and for its further development.
jet grinding, control, model, acoustic signals, amplitude, frequency, quality, finished product
1. Andreev E. E., Tikhonov O. N. Raw Material Crushing, Grinding, and Dressing Preparation. Saint Peresburg: Saint Petersburg Mining University, 2007. 439 pp. (in Russian).
2. Pryadko N. S. Development of the Theory of Mineral Product Fine Grinding: D. Sc. thesis synopsis: 05.15.08, National Mining University. Dnipropetrovsk, 2015. 36 pp. (in Russian).
3. Pivnyak G. G., Pilov P. I., Pryadko N. S. Decrease of power consumption in fine grinding of minerals. Mine Planning and Equipment Selection. C. Drebenstedt and R. Singhal (Eds.). Switserland: Springer International Publishing, 2014. Pp. 1069-1079.
https://doi.org/10.1007/978-3-319-02678-7_104
4. Lynch A. J. Cycles of Crushing and Grinding. Simulation, Optimization, Design, and Control. Moscow: Nedra, 1981. 343 pp. (in Russian).
5. Uteush E. V., Uteush Z. V. Grinding Plant Control. Moscow: Mashinostroyeniye, 1973. 280 pp. (in Russian).
6. Maryuta A. N. Automatic Optimization of the Ore Dressing Process at Magnetic Dressing Works. Moscow: Nedra, 1975. 231 pp. (in Russian).
7. Chernousko F. L., Kolmanovsky V. B. Optimal Control under Random Perturbations. Moscow: Nauka, 1978. 351 pp. (in Russian).
8. Gommeren H.J.C., Heitzmann D.A., Moolenaar J.A.C., Scarlett B. Modelling and control of jet mill plant Powder Technology. 2000. No. 108. Pp. 147 - 154.
https://doi.org/10.1016/S0032-5910(99)00213-2
9. Gorobets V. I. Parameter Optimization and the Development of a Method for Automatic Control of a Gas-Jet Mill: Ph. D. thesis synopsis: 05.13.07, National Mining University. Dnepropetrovsk, 1972. 21 pp. (in Russian).
10. Ternovaya E. V. Bulk material in-flow grinding and transportation signal frequency analysis. Zbahachennia Korysnykh Kopalyn. 2016, No. 63 (104). Pp. 59 - 65. (in Russian).
11. Muzyka L. V., Pryadko N. S. Jet mill operation simulation and control. Proceedings of the 9th International Conference "Young Scientists 2018: from Theory to Practice (February 16, 2018, National Metallurgy Academy of Ukraine. Dnipro). Pp. 194-197. (in Russian).
12. Pryadko N. S., Ternovaya E. V. Establishing the possibility of assessing the bulk material fractional composition from the frequency characteristics of acoustic signals in the flow. Zbahachennia Korysnykh Kopalyn. 2017. No. 67 (108). Pp. 161-168. (in Russian).
DOI:
https://doi.org/10.15407/itm2018.02.113
Copyright (©) 2018 Pryadko N. S., Strelnykov G. A., Muzyka L. V.
Copyright © 2014-2018 Technical mechanics
____________________________________________________________________________________________________________________________
|
GUIDE FOR AUTHORS
 |