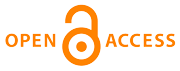 |
Home
>
Journal Issues
>
No 2 (2019) Technical mechanics
>
10
___________________________________________________
UDC 621.002.56
Technical mechanics, 2019, 2, 102 - 112
MAGNETRON FORMATION AND USE OF INTENSIVE GAS-METAL PLASMA FLOWS
DOI:
https://doi.org/10.15407/itm2019.02.102
Gryshkevych O. D., Hryniuk S. I.
Gryshkevych O. D.
Institute of Technical Mechanics
of the National Academy of Sciences of Ukraine and the State Space Agency of Ukraine
Hryniuk S. I.
Institute of Technical Mechanics
of the National Academy of Sciences of Ukraine and the State Space Agency of Ukraine
This paper states that the surface strengthening of a machine part structural material by the physical action
of concentrated energy flows on the surface under treatment is the most universal and effective method
for maximizing the function and performance indices. The paper considers surface treatment technologies
based on the use of a high-energy gas-metal plasma flow generated by an abnormal glow discharge with closed
electron drift. Gas-metal plasma is used in modifying a surface working metal layer and in depositing
a nanostructured functional coating. In this work, gas-metal plasma was generated using an unbalanced
magnetron sputtering system operating in the magnetron discharge current frequency modulation mode.
The aim of this work was to develop a plasma process device with a high-current pulsed magnetron discharge (HCPMD)
for generating a high-energy gas-metal plasma flow. The device is designed for an integrated treatment
of friction pair working surfaces. The strengthening is achieved by a surface modification of the structural
material via high-intensity low-energy ion nitriding followed by the deposition of a nanostructured functional
coating. It was shown by experiment that an HCPMD is suitable for generating a high-energy gas-metal plasma
flow thus assuring a high-quality strengthening of the structural material surface. The device is designed
for performing all stages of ion-plasma treatment in a single vacuum cycle.
The spatial characteristics of a gas-metal plasma flow were studied, and it was shown that the device developed
is more efficient for a local treatment of tube-type friction pair working surfaces. The local parameters
of an HCPMD plasma in the vicinity of the surface under treatment were studied. Samples treated by combined
strengthening that includes preliminary plasma beam nitriding and the final deposition of a nanostructured
functional coating were prepared. It was shown that surface treatment in the HCPMD mode results in performance
characteristics superior to those obtained when the magnetron device operates in the stationary discharge mode.
physical vapor deposition (PVD), high-intensity low-energy ion implantation, high-current pulsed magnetron discharge (HCPMD),
planar magnetron sputtering system, cylindrical magnetron sputtering system, pulsed discharge power source
1. Stepanova T. Yu. Machine Component Surface Strengthening Technologies. Ivanovo: Ivanovo State University of Chemistry and Technology, 2009. 64 pp. (in Russian).
2. Sulima V. A., Shulov Yu. D., Yagodkin Yu. D. Machine Component Surface Layer and Service Properties. Moscow: Mashinostroyeniye, 1988. 240 pp. (in Russian).
3. Novikov N. V., Bidnyi A. A., Liashenko B. A. et al. Machine component surface strengthening methods. Kiev: Institute for Superhard Materials, 1989. Pp. 64-65. (in Russian).
4. Svadkovsky I. V. Lines of Magnetron Sputtering System Development. Doklady BGUIR. 2007. No. 2(18). Pp. 112-121. (in Russian).
5. Panin V. E., Sergeev V. P., Panin A. V. Structural Material Surface Layer Nanostructuring and Nanostructured Coating Deposition. Tomsk: Tomsk Polytechnic University, 2010. 254 pp.
6. Kadyrzhanov K. K. Ion-Beam and Ion-Plasma Material Modification (in Russian). Moscow: Moscow State University, 2005. 640 pp. (in Russian).
7. Kuzmichev A. I. Pulsed Magnetron Sputtering Systems. Proceedings of the ISTFE-14 Kharkiv Scientific Assembly. Kharkiv: Kharkiv Institute of Physics and Technology, 2014. Pp. 221-244. (in Russian).
8. Granovsky V. L. Electric Current in a Gas. Steady-State Current. Moscow: Nauka, 1971. 543 pp. (in Russian).
9. Mozgrin D. V., Fetisov I. K., Khodachenko G. V. Experimental study of high-current forms of a quasi-steady-state low-pressure discharge in a magnetic field. Fizika Plazmy. 1995. V. 21. No. 5. Pp. 422-433. (in Russian).
10. Aksenov I. I., Andreev A. A., Belous V. A. et al. Vacuum Arc: Plasma Sources, Coating Deposition, and Surface Modification. Êyiv: Naukova Dumka, 2012. 727 pp. (in Russian).
11. Ehiasarian A. P., Wen J. G., Petrov I. Interface microstructure engineering by high power impulse magnetron sputtering for the enhancement of adhesion. Journal of Applied Physics. 2007. V. 101. No. 5. 054301.
https://doi.org/10.1063/1.2697052
12. Belyi A. V., Kukareko V. A., Lobodaeva O. V. et al. Ion-Beam Treatment of Metals, Alloys, and Ceramics. Minsk: FTI, 1998. 218 pp. (in Russian).
13. Musil J., Suna J. The role of energy in formation of sputtered nanocomposite films. Mater. Scien. Forum. 2005. V. 502. Pp. 239-260.
https://doi.org/10.4028/www.scientific.net/MSF.502.291
14. Boitsov A. G., Mashkov N. V., Smolentsev V. L. Part Surface Strengthening by Combined Methods. Moscow: Mashinostroyeniye, 1991. 144 pp. (in Russian).
15. Sochugov N. S., Oskirko V. O., Spirin P. E. A power supply for magnetron sputtering systems. Instrum. Exp. Tech. 2013. V. 56. No. 2. Pp. 178-184.
https://doi.org/10.1134/S0020441213010302
16. Patent for Utility Model 102744 Ukraine, IPC Ñ23Ñ 14/00. Unbalanced cylindrical magnetron sputtering system. Gryshkevych O. D.; applicant and patentee the Institute of Technical Mechanics of the National Academy of Sciences of Ukraine and the State Space Agency of Ukraine; filed Oct. 28, 2013; published Jan. 24, 2014; Bul. No. 1. (in Ukrainian).
17. Gryshkevych O. D., Hryniuk S. I., Kuchugurnyi Yu. P. Plasma process equipment based on closed electron drift discharge. Teh. Meh. 2013. No. 4. Pp. 43-57. (in Russian).
18. Rogov A. V., Kapustin Yu. V., Martynenko Yu. V. Factors determining the efficiency of magnetron sputtering. Optimization criteria. Technical Physics. 2015. V. 60. No. 2. Pp. 283-291.
https://doi.org/10.1134/S1063784215020206
19. Ershov A. P. Method of Electric Langmuir Probes. Moscow: Moscow State University Faculty of Physics, 2007. 26 pp. (in Russian).
20. Podgorny I. M. Lectures on Plasma Diagnostics. Moscow: Atomizdat, 1968. 220 pp. (in Russian).
21. Kagan Yu. M., Perel' V. I. Probe methods in plasma research. Sov. Phys. Usp. 1964. V. 6. No. 6. Pp. 767-793.
https://doi.org/10.1070/PU1964v006n06ABEH003611
22. Kouznetsov V., Macak K., Schneider J. M., Helmersson U., Petrov I. A novel pulsed magnetron sputter technique utilizing very high target power densities. Surf. Coat. Technol. 1999. V. 122. Iss. 2-3. Pp. 290-293.
https://doi.org/10.1016/S0257-8972(99)00292-3
23. Poolcharuansin P., Bowes M., Petty T. J., Bradley J. W. Ionized metal ?ux fraction measurements in HiPIMS discharges. J. Phys. D: Appl. Phys. 2012. V. 45. No. 32. Pp. 1-5.
https://doi.org/10.1088/0022-3727/45/32/322001
DOI:
https://doi.org/10.15407/itm2019.02.102
Copyright (©) 2019 Gryshkevych O. D., Hryniuk S. I.
Copyright © 2014-2019 Technical mechanics
____________________________________________________________________________________________________________________________
|
GUIDE FOR AUTHORS
====================
Open Access Policy
====================
REGULATIONS
on the ethics of publications
====================
|