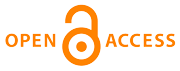 |
Home
>
Journal Issues
>
No 4 (2021) Technical mechanics
>
13
___________________________________________________
UDC 622.232.72:004.942
Technical mechanics, 2021, 4, 137 - 149
Gas mass flow control in jet equipment
DOI:
https://doi.org/10.15407/itm2021.04.137
Pryadko N. S., Yhnatev A. D., Shevelova H. M., Ternova K. V.
Pryadko N. S.
Institute of Technical Mechanics of the National Academy of Sciences of Ukraine and the State Space Agency of Ukraine
Yhnatev A. D.
Institute of Technical Mechanics of the National Academy of Sciences of Ukraine and the State Space Agency of Ukraine
Shevelova H. M.
Institute of Technical Mechanics of the National Academy of Sciences of Ukraine and the State Space Agency of Ukraine
Ternova K. V.
Institute of Technical Mechanics of the National Academy of Sciences of Ukraine and the State Space Agency of Ukraine
Based on a numerical simulation of gas flows in an ejector unit and an analysis of grinding chamber
acoustic signals, this paper shows ways to increase the efficiency of jet grinding. To prevent
ejector speed-up tube wear and to obtain a ground product without impurities, the effect of feeding
an additional energy carrier flow on the flow pattern in the speed-up tube of a jet mill was
studied. A comparative analysis of the ejector flow pattern as a function of the presence of an
additional feed and the speed-up tube shape was carried out. It was shown that the use of a conical
nozzle offers a more uniform flow at the ejector outlet. The additional energy carrier feed provides
a uniform increase in flow speed and reduces speed-up tube wall wear. The acoustic signals of the
mill working zones were related to the jet grinding process parameters, around which a ground
product quality control method was developed. The paper presents a technique for determining the
material particle size in the energy carrier flow from the results of acoustic monitoring of the
process. The technique uses the established relationship between the dispersion of the acoustic
signal characteristic frequency and the mass of the corresponding fracture of the mixture in
in-flow material transportation. The technique speeds up material particle size determination and
improves the finished product quality. An automatic system was developed to control the grinding
process by controlling the loading process according to the characteristics of the grinding zone
acoustic signals. An operating model of a controlled hopper of a gas jet mill was made. The
operability of the control system was verified on a simulation model, which includes a control
objet (mill) model and a control system model. It was shown that the system of mill loading
automatic control by the characteristics of the grinding zone acoustic signals offers an up to
10 percent increase in mill capacity, which was verified in industrial conditions at Vilnohorsk
Mining and Metallurgical Plant.
gas jet mill, nozzle, ejector, acoustic signals, efficiency, control
1. Zhao X., Zhu H., Zhang G., Tang W. Effect of superfine grinding on the physicochemical properties and antioxidant activity of red grape pomace powders. Powder Technol. 2015. No. 286. Pð .838-844.
https://doi.org/10.1016/j.powtec.2015.09.025
2. Pryadko N. S., Ternova K. V. Acoustic monitoring of jet grinding. Akademperiodyka, 2020. 192 pp.
https://doi.org/10.15407/akademperiodyka.409.192
3. Ali M., Lin L. Optimisation and analysis of bead milling process for preparation of highly viscous, binder-free dispersions of carbon black pigment. Prog. Org. Coat. 2018. No. 119. Pp. 1-7.
https://doi.org/10.1016/j.porgcoat.2018.02.007
4. Pryadko N., Muzyka L., Strelnikov H., Ternova K. Acoustic method of jet grinding study and control. Essays of Mining Science and Practice. 2019. Pð. 1-11.
https://doi.org/10.1051/e3sconf/201910900074
5. Sheveleva A. M. Methods for finished product quality improvement in jet grinding, Zbahachennia Korysnykh Kopalyn. 2018. No. 69 (110). Pp. 86-94. (in Russian).
6. Kong F., Kim H. Analytical and computational studies on the performance of a two-stage ejector diffuser system. Int. J. Heat Mass Transf. 2015. V. 85. Pp. 71-87.
https://doi.org/10.1016/j.ijheatmasstransfer.2015.01.117
7. Barakovskikh D. S., Shishkin S. F., Shishkin A. S. Particle motion in a jet mill speed-up tube. Vestnik Belgorodskogo Gosudarstvennogo Tekhnicheskogo Universiteta im. V. G. Shukhova. 2017. No. 5. Pp. 82-88. (in Russian).
8. Rao S. M.V., Jagadeesh G. Novel supersonic nozzles for mixing enhancement in supersonic ejectors. Applied Thermal Engineering. 2014. No. 71. Pp. 62-71.
https://doi.org/10.1016/j.applthermaleng.2014.06.025
9. Ameur K., Aidoun Z., Ouzzane M. Modeling and numerical approach for the design and operation of two-phase ejectors. Applied Thermal Engineering. 2016. No. 109. Pp. 809-818.
https://doi.org/10.1016/j.applthermaleng.2014.11.022
10. Barakovskikh D. S., Shishkin S. F. External-pressure ejector jet mill. Industrial Production and Metallurgy: Proceedings of the International Scientific and technical Conference. 2020. Pp. 14-19. (in Russian).
11. Ihnatev O. D., Shevelova H. M. Effect of the location of a gas flow control element in an ejector unit on the flow pattern. Teh. Meh. 2020. No. 3. Pp. 54-63. (in Ukrainian).
https://doi.org/10.15407/itm2020.03.054
12. Sheveleva A. M., Ihnatev A. D. Calculation of the ejector velocity field with an additional energy feed along the speed-up tube axis. Zbahachennia Korysnykh Kopalyn. 2019. No. 73 (114). Pp. 92-98. (in Russian).
13. Zhiyong Gaoa, Ruiying Fana, John Ralstonc, Wei Suna, Yuehua Hu Zhiyong Gaoa, Ruiying Fana, John Ralstonc, Wei Suna, Yuehua Hu. Surface broken bonds: An efficient way to assess the surface behaviour of fluorite. Minerals Engineering. 2019. No. 130. Pð. 15-23.
https://doi.org/10.1016/j.mineng.2018.09.024
14. Tkachev V. V., Bublikov A. V. Simulation Study of a Cutter Loader Automatic Control System. National Mining University, 2015. 182 pp. (in Russian).
15. Reshmin B. I. Simulation Study and Control Systems. Info-Inzheneriya. 2016. 74 pp. (in Russian).
Copyright (©) 2021 Pryadko N. S., Yhnatev A. D., Shevelova H. M., Ternova K. V.
Copyright © 2014-2021 Technical mechanics
____________________________________________________________________________________________________________________________
|
GUIDE FOR AUTHORS
====================
Open Access Policy
====================
REGULATIONS
on the ethics of publications
====================
|