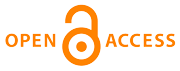 |
Home
>
Journal Issues
>
No 1 (2022) Technical mechanics
>
5
___________________________________________________
UDC 539.3
Technical mechanics, 2022, 1, 42 - 50
Experimental and numerical analysis of the stress state of honeycombs made by additive technologies
DOI:
https://doi.org/10.15407/itm2022.01.042
Derevianko I. I., Uspensky B. V., Avramov K. V., Salenko O. F.
Derevianko I. I.
A. Pidgorny Institute of Mechanical Engineering Problems of the National Academy of Sciences of Ukraine,
Yuzhnoye State Design Office
Uspensky B. V.
A. Pidgorny Institute of Mechanical Engineering Problems of the National Academy of Sciences of Ukraine
Avramov K. V.
A. Pidgorny Institute of Mechanical Engineering Problems of the National Academy of Sciences of Ukraine,
Kharkiv National University of Radio Electronics
Salenko O. F.
4National Technical University of Ukraine "Igor Sikorsky Kyiv Polytechnic Institute"
This paper proposes an approach to the experiment-and-calculation analysis of the tension of honeycombs made
by FDM additive technologies. The approach includes experimental tension analysis. Tension tests of honeycombs
were conducted on a certified TiraTest 2300 universal tension testing machine. To do this, sets of honeycomb
samples were prepared. The method of honeycomb manufacturing by FDM additive technologies is described. The
vertices of a honeycomb cell row are fixed in the vise-type clamps of the tension testing machine. The
experimental analysis is accompanied by a numerical finite-element simulation of tension tests. To simulate
honeycomb tension, nine mechanical characteristics of the material in material axes must be known. These
nine parameters are considered in the paper. A direct finite-element simulation of a honeycomb with account
for the deformation of all its cells was performed. To provide the uniformity of sample deformation in a
physical experiment, the sample is loaded by setting the displacement of one of its ends to a constant
value. In doing so, the other end is clamped. As follows from the experimental analysis, before failure
the honeycomb cell end displacements are comparable with the honeycomb cell thickness. Because of this,
the geometrically nonlinear deformation of the honeycomb cells in tension is accounted for in the
calculations, and a nonlinear problem is solved using ANSYS. The direct simulation of honeycombs and the
analysis of their homogenized model give different results. In the direct simulation of honeycombs, they
are considered as thin-walled beams working in bending. In this case, the geometrical nonlinearity
contributes significantly to the structural deformation. For plate tension (homogenized model), the
contribution of the geometrical nonlinearity is very small, Because of this, the stress-strain response
is close to linear.
honeycomb structure, additive technologies, tension, stress-strain response
1. Matthews N. Additive Metal Technologies for Aerospace Sustainment. Aircraft Sustainment and Repair. 2018. Pp. 845-862.
https://doi.org/10.1016/B978-0-08-100540-8.00015-7
2. Boparai K.S., Singh R. Advances in Fused Deposition Modeling. Reference Module in Materials Science and Materials Engineering. 2017. DOI: 10.1016/B978-0-12-803581-8.04166-7.
https://doi.org/10.1016/B978-0-12-803581-8.04166-7
3. Byberg K. I., Gebisa A. W., Lemu H. G. Mechanical properties of ULTEM 9085 material processed by fused deposition modeling. Polymer Testing. 2018. V. 72. Pp. 335-347.
https://doi.org/10.1016/j.polymertesting.2018.10.040
4. Ahn S.-H., Montero M., Odell D., Roundy S., Wright P. K. Anisotropic material properties of fused deposition modeling ABS. Rapid Prototyping Journal. 2002. V. 8. No. 4. Pp. 248-257.
https://doi.org/10.1108/13552540210441166
5. Gerisa A.W., Lenu H.G. Influence of 3D printing process parameters on tensile properties of ULTEM 9085. Procedia Manufacturing. 2019. V. 30. Pp. 331-338.
https://doi.org/10.1016/j.promfg.2019.02.047
6. Motaparti K. P., Taylor G., Leu M. C., Chandrashekhara K., Castle J., Matlack M. Effects of build parameters on compression properties for ULTEM 9085 parts by fused deposition modeling. Solid Freeform Fabrication 2016: Proceedings of the 26th Annual International Solid Freeform Fabrication Symposium - An Additive Manufacturing Conference. 2016. Pp. 964-977.
7. Popescu D., Zapciu A., Amza C., Baciu F., Marinescu R. FDM process parameters influence over the mechanical properties of polymer specimens: A review. Polymer Testing. 2018. V. 69. Pp. 157-166.
https://doi.org/10.1016/j.polymertesting.2018.05.020
8. Zaldivar R.J., Witkin D.B., McLouth T., Patel D.N., Schmitt K., Nokes J.P. Influence of processing and orientation print effects on the mechanical and thermal behavior of 3D-printed ULTEM® 9085 material. Additive Manufacturing. 2016. V. 13. No.1. Pp. 71-80.
https://doi.org/10.1016/j.addma.2016.11.007
9. Dizon J. R. C., Espera A. H., Chen Q., Advincula R. C. Mechanical characterization of 3D-printed polymers. Additive Manufacturing. 2018. V. 20. Pp. 44-67.
https://doi.org/10.1016/j.addma.2017.12.002
10. Kucewicz M., Baranowski P., Stankiewicza M., Konarzewskia M., Platekb P., Malachowskia J. Modelling and testing of 3D printed cellular structures under quasi-static and dynamic conditions. Thin-Walled Structures. 2019. V. 145. 106385.
https://doi.org/10.1016/j.tws.2019.106385
11. Li S., Liu Z., Shim V.P.W., Guo Y., Sun Z., Li X., Wang Z. In-plane compression of 3D-printed self-similar hierarchical honeycombs - Static and dynamic analysis. Thin-Walled Structures. 2020. V. 157. 106990.
https://doi.org/10.1016/j.tws.2020.106990
12. Bhandaria S., Lopez-Anido R. Finite element analysis of thermoplastic polymer extrusion 3D printed material for mechanical property prediction. Additive Manufacturing. 2018. V. 22. Pp. 187-196.
https://doi.org/10.1016/j.addma.2018.05.009
13. Derevianko I., Avramov K., Uspensky B., Salenko A. Experimental analysis of the mechanical characteristics of launch vehicle parts manufactured by FDM additive technologies. Teh. Meh. 2021. No. 1. Pp. 92-100. (in Ukrainian).
https://doi.org/10.15407/itm2021.01.092
Copyright (©) 2022 Derevianko I. I., Uspensky B. V., Avramov K. V., Salenko O. F.
Copyright © 2014-2022 Technical mechanics
____________________________________________________________________________________________________________________________
|
GUIDE FOR AUTHORS
====================
Open Access Policy
====================
REGULATIONS
on the ethics of publications
====================
|