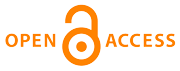 |
Home
>
Journal Issues
>
No 2 (2020) Technical mechanics
>
5
___________________________________________________
UDC 539.3
Technical mechanics, 2020, 2, 57 - 65
NUMERICAL SIMULATION OF THE RUPTURE OF A CONICAL SHELL BY THE EXPLOSION OF A TAPE CHARGE
DOI:
https://doi.org/10.15407/itm2020.02.057
Breslavsky D. V., Sienko A. V., Tatarinova O. A., Chernobryvko M. V., Avramov K. V.
Breslavsky D. V.
National Technical University “Kharkiv Polytechnic Institute”, Ministry of Education and Science of Ukraine
Sienko A. V.
National Technical University “Kharkiv Polytechnic Institute”, Ministry of Education and Science of Ukraine
Tatarinova O. A.
National Technical University “Kharkiv Polytechnic Institute”, Ministry of Education and Science of Ukraine
Chernobryvko M. V.
A. Pidgorny Institute of Mechanical Engineering Problems
Avramov K. V.
National Technical University “Kharkiv Polytechnic Institute”, Ministry of Education and Science of Ukraine
A. Pidgorny Institute of Mechanical Engineering Problems
This paper considers the problem of the destruction of a thin closed truncated conical shell loaded along the
generatrix with a tape explosive charge. The problem simulates rocket head separation. The total stress and
strain field in the shell under nonstationary loading is determined by the finite-element method and used
as initial conditions for the analysis of the destruction of the maximum loaded strip situated along the
generatrix. For the strip, a plane initial-boundary problem of inelastic plastic deformation is solved.
The mathematical model uses a constitutive equation, which includes the plastic flow of the material and
is formulated in terms of inelastic strain rates in the form of strain hardening, and a kinetic equation
for a damage parameter. The dynamic constants of the material were determined from data of complex-stress
experiments. Using finite-element simulation, macrodefect initiation sites are determined, and macrodefect
initiation times are estimated. To implement the proposed mathematical model, software was developed.
The software allows one to refine finite-element schemes with the extraction of the destroyed parts and
to determine crack development times for different loading conditions. The proposed method is verified
by comparing the calculated results with experimental curves of explosive deformation and with a solution
to this problem obtained in the ANSYS finite-element analysis program system based on the Cooper–Symonds
hardening model for a 3D geometric model.
truncated conical shell, tape explosive charge, inelastic plastic deformation, strain hardening, damage parameter, Cooper–Symonds hardening model, finite-element method, shell rupture
1. Cristescu N. Dynamic Plasticity. Amsterdam: North Holland, 2004. 614 pp.
2. Kukydzanov V. N. Numerical Continuum Mechanics. De Gruyter, 2013. 428 pp.
3. Zienkiewicz O. C., Taylor R. L., Wood D. D. The Finite Element Method for Solid and Structural Me-chanics. Butterworth-Heinemann, 2014. 624 pp.
4. Chaboche J. L. A review of some plasticity and viscoplasticity constitutive equations. International Journal of Plasticity. 2008. V. 24. Pp. 1642-1693.
https://doi.org/10.1016/j.ijplas.2008.03.009
5. Erdogan E. Fracture mechanics. International Journal of Solids and Structures. 2000. V. 37. Pp. 171-183.
https://doi.org/10.1016/S0020-7683(99)00086-4
6. Kukudzhanov V. N. Computer Simulation of the Deformation, Damageability, and Failure of Inelastic Materials and Structures. Moscow: MFTI, 2008. 212 pp. (in Russian).
7. Gato C. Detonation-driven fracture in thin shell structures: Numerical studies. Applied Mathematical Modelling. 2010. V. 34. Iss. 12. Pp. 3741-3753.
https://doi.org/10.1016/j.apm.2010.02.011
8. Hudramovych V. S. Simulation of the stress and strain field in shell structures of rocket hardware and power engineering. Teh. Meh. 2013. Pp. 97-104. (in Russian).
9. Pandey V. B., Singh I. V., Mishra B. K., Ahmad S., Rao A. V., Kumar V. Creep crack simulations using continuum damage mechanics and extended finite element method. Int J. of Damage Mech. 2019. V. 28. Iss. 1. Pp. 3-34.
https://doi.org/10.1177/1056789517737593
10. Chernobryvko M., Avramov K., Uspensky B., Tonkonogenko A., Kruszka L. Model of segmentation of rocket fairings due to the action of a cumulative charge. EDP Sciences: EPJ Web of Conferences. 2018. No. 183. 04009. Pp. 1-4.
https://doi.org/10.1051/epjconf/201818304009
11. Breslavsky D., Kozlyuk A., Tatarinova O. Numerical simulation of two-dimensional problems of creep crack growth with material damage consideration. Eastern-European Journal of Enterprise Technolo-gies. Applied Mechanics. 2018. V. 2. No. 7 (92). Pp. 27-33.
https://doi.org/10.15587/1729-4061.2018.119727
12. Martynenko G. Yu., Chernobryvko M. V., Avramov K. V., Martynenko V. G., Tonkonozhenko A. M., Kozharin V. Yu. Numerical simulation of missile payload operation. Teh. Meh. 2018. No. 4. Pp. 90-104. (in Russian).
https://doi.org/10.1016/j.advengsoft.2018.07.001
Copyright (©) 2020 Breslavsky D. V., Sienko A. V., Tatarinova O. A., Chernobryvko M. V., Avramov K. V.
Copyright © 2014-2020 Technical mechanics
____________________________________________________________________________________________________________________________
|
GUIDE FOR AUTHORS
====================
Open Access Policy
====================
REGULATIONS
on the ethics of publications
====================
|