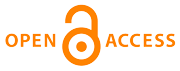 |
Home
>
Journal Issues
>
No 4 (2023) Technical mechanics
>
6
___________________________________________________
UDC 539.3
Technical mechanics, 2023, 4, 60 - 75
COMPUTER SIMULATION OF THE EFFECT OF ANNULAR INCLUSIONS ON THE STRESS CONCENTRATION IN THIN-WALLED CYLINDRICAL AND CONICAL SHELLS WITH CIRCULAR OPENINGS
DOI:
https://doi.org/10.15407/itm2023.04.060
Hart E. L., Semencha O. O.
Hart E. L.
Oles Honchar Dnipro National University
Semencha O. O.
Oles Honchar Dnipro National University
Shell structures are used in various industries, such the aerospace industry, the oil and gas industry, power
engineering, mechanical engineering, construction, etc. Due to their design or manufacturing features, their
integrity may be disrupted by the presence of various openings, around which local stresses develop. Finding
ways to reduce stress concentrations around openings is an important problem in deformable solid mechanics.
This paper presents the results of a computer simulation and a finite-element analysis of the stress and
strain field of thin-walled cylindrical and truncated conical shells with circular openings in the presence
of annular inclusions around them made of a material whose properties differ from the main material of the
shells. The effect of the elastic modulus of an inclusion and its geometric parameters on the stress and
strain concentration in the vicinity of the openings was studied. Several inclusion materials and inclusion
widths were considered. An annular inclusion made of a homogeneous material and located in the shell plane
was considered. Stress and strain intensity distributions in the local stress concentration zones were
calculated. A comparative analysis of the results obtained for cylindrical and conical shells was carried
out. The study showed that the presence of a “soft” homogeneous annular inclusion makes it possible to
reduce the stress concentration around the opening by ~13–35% depending on the inclusion width and elastic
modulus both for a cylindrical and a conical shell. Certain combinations of the geometric and mechanical
parameters of the inclusion give rise to a “mechanical” effect, which consists in shifting the stress
concentration zone from the opening edge to the inclusion – shell material interface. For conical shells,
due to their geometric features, a “conical” effect occurs: the stresses increase not only in the vicinity
of the opening-weakened zone, but also near the cone basis.
thin-walled cylindrical shell, thin-walled truncated conical shell, circular opening, annular inclusion, stress and strain field, stress concentration factor, finite-element meth
1. Avdonin A. S. Applied Methods of Calculation of Shells and Thin-Walled Structures. Moscow, 1969. 402 pp. (in Russian).
2. Avramenko O. O. Analysis of the stress and strain field of non-thin orthotropic conical shells of variable thickness under nonuniform loading. New Materials and Technologies in Metallugry and Mechanical Engineering. 2011. Iss. 2. Pp. 103-107. (in Ukrainian).
3. Bochkarev S. A., Matveyenko V. P. Panel flutter of rotating circular shells in a supersonic gas flow. Computational Continuum Mechanics. 2008. No. 3. Pp. 25-33. (in Russian).
https://doi.org/10.7242/1999-6691/2008.1.3.24
4. Vasiliev V. V. Mechanics of Composite Material Structures. Moscow, 1988. 272 pp. (in Russian).
5. Hart E. L., Semencha O. O. Numerical investigation of the stress and strain field of an elastic trapezoidal plate with a rectangular opening and a tape inclusion. Problems in Computational Mechanics and Structural Strength. Dnipro, 2021. Iss. 33. Pp. 43-54. (in Ukrainian).
6. Golda Yu. L., Preobrazhensky I. N., Shtukarev V. S. Experimental study of the stability of shells with openings. International Applied Mechanics. 1973. V. 9. Pp. 27-32. (in Russian).
https://doi.org/10.1007/BF00888695
7. Grigorenko Ya. M., Molchenko L. V. Theory of Plates and Shells. Kyiv, 1993. 232 pp. (in Ukrainian).
8. Grigorenko Ya. M., Vlaykov G. G. Grigorenko A. Ya. Numerical-Analytical Solution of Problems of Shell Mechanics Based on Various Models. Kyiv, 2006. 472 pp. (in Russian).
9. Guz A. N., Chernyshenko I. S. et al. Theory of Opening-Weakened Thin Shells. Kyiv, 1980. 636 pp. (in Russian).
10. Savin G. N. Stress Distribution around Openings. Kyiv, 1968. 888 pp. (in Russian).
11. Storozhuk E. A.,Maksymyuk V. A., Chernyshenko I. S. Stress concentration in the region of a rectangular opening on the side surface of a nonlinear elastic orthotropic conical shell. Dopov. Nats. Akad. Nauk Ukr. 2019. Iss. 11. Pp. 41-48. (in Ukrainian).
https://doi.org/10.15407/dopovidi2019.11.041
12. Chernobryvko M. V., Avramov K. V., Batutina T. V., Degtyarenko P. G., Tonkonozhenko A. M., Suleymenov U. S. Dynamic instability of stiffened conic fairings for launch vehicles in supersonic gas flow // Teh. Meh. 2015. No. 1. Pp. 15-29. (in Russian).
13. Darvizeh M., Haftchenari H., Darvize A., Ansari R., Sharma C. B. The effect of boundary conditions on the dynamic stability of orthotropic cylinders using a modified exact analysis. Composite Structures. 2006. V. 74. Pp. 495-502.
https://doi.org/10.1016/j.compstruct.2005.05.004
14. Han X., Xu D., Liu G. R. Transient responses in a functionally graded cylindrical shell to a point load. Journal of Sound and Vibration. 2002. V. 251 Iss. 5. Pp. 783-805.
https://doi.org/10.1006/jsvi.2001.3997
15. Hua L., Lam K. Y. Orthotropic influence on frequency characteristics of a rotating composite laminated conical shell by the generalized differential quadrature method. Int. J. of Solids and Structures. 2001. V. 38. Pp. 3995-4015.
https://doi.org/10.1016/S0020-7683(00)00272-9
16. Zienkiewicz O. C., Teylor R. L. The Finite Element Method for Solid and Structural Mechanics. New York: Elsevier, 2005. 632 pp.
Copyright (©) 2023 Hart E. L., Semencha O. O.
Copyright © 2014-2023 Technical mechanics
____________________________________________________________________________________________________________________________
|
GUIDE FOR AUTHORS
====================
Open Access Policy
====================
REGULATIONS
on the ethics of publications
====================
|