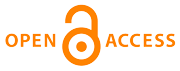 |
Home
>
Journal Issues
>
No 3 (2023) Technical mechanics
>
8
___________________________________________________
UDC 539.3
Technical mechanics, 2023, 3, 88 - 97
STATIC STABILITY OF SANDWICH PANELS WITH HONEYCOMB CORES MADE BY ADDITIVE TECHNOLOGIES
DOI:
https://doi.org/10.15407/itm2023.03.088
Chernobryvko M. V., Avramov K. V., Uspenskyi B. V., Marshuba I. S.
Chernobryvko M. V.
A. Pidgorny Institute of Mechanical Engineering Problems of the National Academy of Sciences of Ukraine
Avramov K. V.
A. Pidgorny Institute of Mechanical Engineering Problems of the National Academy of Sciences of Ukraine
Uspenskyi B. V.
A. Pidgorny Institute of Mechanical Engineering Problems of the National Academy of Sciences of Ukraine
Marshuba I. S.
A. Pidgorny Institute of Mechanical Engineering Problems of the National Academy of Sciences of Ukraine
This paper presents approaches to and the results of finite-element analysis of static buckling in cylindrical
sandwich panels. The core layer of the panels is a polylactide honeycomb core 3D printed using the Fused
Deposition Modeling (FDM) additive technology. The two thin face layers are made of carbon fiber reinforced
polymer. Such structures are promising for use as structural elements of rockets and drones. For them, the
determination of stability under longitudinal and radial loads is an important issue. The global buckling of
a cylindrical panel under longitudinal loads and the local buckling of a honeycomb core as a plate structure
under radial loads are studied. The geometrically nonlinear deformation of a cylindrical panel under a
combination of transverse and radial loads is studied. Seven cylindrical sandwich panels with the
radius-to-thickness ratio in the range 5 ? R/h ? 50 and a sandwich plate are considered. The effect of the
radius of curvature on the characteristics of local and global buckling is investigated.
The problem is solved by the finite element method using the ANSYS software system. The convergence of the
finite element model was investigated. For this purpose, a strained state under the action of a longitudinal
load was studied. The finite-element mesh parameters were selected to ensure the convergence of the results.
Two finite element models, an “exact” one and an “approximate” one, were constructed to investigate global
buckling under longitudinal loads. The «exact» model includes a honeycomb core represented by its geometry.
In the «approximate» model of the sandwich panel, the honeycomb core is replaced with an equivalent homogenized layer.
It was found that for longitudinal loads the modes of the global buckling of the cylindrical sandwich panels
and the sandwich plate under study are almost the same. It was shown that the critical loads obtained by the
«exact» and the «approximate» model are close. It was found that when a cylindrical panel is deformed under
the action of a combination of longitudinal and radial subcritical loads, the calculated results for the
«exact» and the «approximate» model are close. Therefore, longitudinal buckling can be considered using the
homogenized model, which is much simpler in terms of computations.
cylindrical sandwich panel, honeycomb core, additive technologies, finite element method (FEM), buckling
1. Lan X.-k., Huang Q., Zhou T., Feng S.-s. Optimal design of a novel cylindrical sandwich panel with double arrow auxetic core under air blast loading. Def. Technol. 2020. V. 16. Pp. 617-626.
https://doi.org/10.1016/j.dt.2019.09.010
2. Martynenko G., Avramov K., Martynenko V., Chernobryvko M., Tonkonozhenko A., Kozharin V. Numerical simulation of warhead transportation. Def. Technol. 2021. V. 17. No. 2. Pp. 478-494.
https://doi.org/10.1016/j.dt.2020.03.005
3. Farshad M. Design and analysis of shell structures. Solid Mech. Appl. 1992. V 16. 424 pp.
https://doi.org/10.1007/978-94-017-1227-9
4. Ciccarelli D., Forcellese A., Greco L., Mancia T., Pieralisi M., Simoncini M., Vit A. Buckling behavior of 3D printed composite isogrid structures. Procedia CIRP. 2021. V. 99. Pp. 375-380.
https://doi.org/10.1016/j.procir.2021.03.053
5. Franzoni F., Gliszczynski A., Baciu T., Arbelo M. A., Degenhardt R. Enhanced vibration correlation technique to predict the buckling load of unstiffened composite cylindrical shells. J. Sound Vib. 2022. V. 539. No. 2. 117280.
https://doi.org/10.1016/j.jsv.2022.117280
6. Franzoni F., Odermann F., Wilckens D., Skuk E.? Kalnin K.? Arbelo M.A., Degenhardt R. Assessing the axial buckling load of a pressurized orthotropic cylindrical shell through vibration correlation technique. Thin-Walled Struct. 2019. V. 137. Pp. 353-366.
https://doi.org/10.1016/j.tws.2019.01.009
7. Franzoni F., Degenhardt R., Albus J., Arbelo M. A. Vibration correlation technique for predicting the buckling load of imperfection-sensitive isotropic cylindrical shells: an analytical and numerical verification. Thin-Walled Struct. 2019. V. 140. Pp. 236-247.
https://doi.org/10.1016/j.tws.2019.03.041
8. Salloomi K. N., Sabri L. A., Hamad Y. M., Al-Sumaidae S. Nonlinear buckling analysis of steel cylindrical shell with elliptical cut-out subjected to longitudinal compressive load. Int. J. Automot. Mech. V. 16. No. 2. Pp. 6723-6737.
https://doi.org/10.15282/ijame.16.2.2019.19.0506
9. Taheri-Behrooz F., Omidi M., Shokrieh M. M. Experimental and numerical investigation of buckling behaviour of composite cylinders with cutout. Thin-Walled Struct. 2017. V. 116. Pp. 136-144.
https://doi.org/10.1016/j.tws.2017.03.009
10. Gibson L. J., Ashby M. F., Schajer G. S., Robertson C. I. The mechanics of two-dimensional cellular materials. Proc. R. Soc. A. 1982. V. 382. Pp. 25-42.
https://doi.org/10.1098/rspa.1982.0087
11. Chen Y., Hu H. In-plane elasticity of regular hexagonal honeycombs with three different joints: A comparative study. Mech. Mater. 2020. V. 148. 103496.
https://doi.org/10.1016/j.mechmat.2020.103496
12. Romanova T., Stoyan Y., Pankratov A., Litvinchev I., Avramov K., Chernobryvko M., Yanchenvskyi I., Mozgova I., Bennell J. Optimal layout of ellipses and its application for additive manufacturing. Int. J. Prod. Res. 2021. V. 59. No.2. Pp. 560-575.
https://doi.org/10.1080/00207543.2019.1697836
13. Casavola C., Cazzato A., Moramarco V., Pappalettere C. Orthotropic mechanical properties of fused deposition modelling parts described by classical laminate theory. Mater. Des. 2016. V. 90. Pp. 453-458.
https://doi.org/10.1016/j.matdes.2015.11.009
14. Derevianko I., Uspensky B., Avramov K., Salenko A., Maksymenko-Sheiko K. Experimental and numerical analysis of mechanical characteristics of fused deposition processed honeycomb fabricated from PLA or ULTEM 9085. J. Sandwich Struct. Mater. 2023. V. 25. No. 2. Pp. 264-283.
https://doi.org/10.1177/10996362221137292
15. Catapano A., Montemurro M. A multi-scale approach for the optimum design of sandwich plates with honeycomb core. Part I: Homogenisation of core properties. Compos. Struct. 2014. V. 118. Pp. 664-676.
https://doi.org/10.1016/j.compstruct.2014.07.057
Copyright (©) 2023 Chernobryvko M. V., Avramov K. V., Uspenskyi B. V., Marshuba I. S.
Copyright © 2014-2023 Technical mechanics
____________________________________________________________________________________________________________________________
|
GUIDE FOR AUTHORS
====================
Open Access Policy
====================
REGULATIONS
on the ethics of publications
====================
|