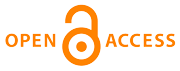 |
Home
>
Journal Issues
>
No 3 (2020) Technical mechanics
>
6
___________________________________________________
UDC 621.926, 533.17
Technical mechanics, 2020, 3, 54 - 63
EFFECT OF THE LOCATION OF A GAS FLOW CONTROL ELEMENT IN AN EJECTOR UNIT ON THE FLOW PATTERN
DOI:
https://doi.org/10.15407/itm2020.03.054
Ihnatev O. D., Shevelova H. M.
Ihnatev O. D.
Institute of Technical Mechanics of the National Academy of Sciences of Ukraine and the State Space Agency of Ukraine
Shevelova H. M.
Institute of Technical Mechanics of the National Academy of Sciences of Ukraine and the State Space Agency of Ukraine
This article is devoted to a numerical simulation of the flow in a jet mill ejector equipped with a gas flow
control element. This element is a channel wherefrom an additional gas flow enters the accelerating tube
of the ejector. The gas flows in the mill ejector are controlled using the energy of additional gas flows,
thus increasing the velocity of the main flow at the outlet of the ejector accelerating tube and producing
a protective layer around the tube walls to prevent their wear. At the same time, there is no substantiation
for the choice of optimal control parameters, a methodology, or scientific methods for gas flow control
in the ejector channels. The purpose of this work is to investigate the effect of the location of the gas
flow control element on gas-dynamic ejector performance and the flow pattern in the ejector channels.
A numerical study was carried out using the Ansys Fluent software package and the SST k-? turbulence model.
In the course of the study, the pressure of the additional gas flow and the distance from the accelerating
tube inlet to the energy carrier supply channel were varied. The angle of the additional gas flow was 20 ?.
The numerical simulation gave flow patterns in the ejector as a function of the location of the gas flow
control element. Streamlines of the additional gas flow were constructed. The article presents the average
flow velocity at the accelerating tube outlet and the energy carrier flow rate as a function of the pressure
of the additional flow of the energy carrier and the location of the gas flow control element and the maximum
values of the average outlet velocity for given pressure ranges. The article substantiates the choice of the
gas flow control parameters that maximize the velocity of the mixed flow at the accelerating tube outlet
at a minimum gas flow rate. The results may be used in improving material processing technologies.
control elements, ejector unit, numerical simulation, additional gas flow
1. Nikulin O. F., Titenko O. M. Mathematical model of two-phase flow in an accelerator channel. Proceedings of the National Aviation University. 2010. V. 42. No.1. Pp. 65-69. (in Ukrainian).
https://doi.org/10.18372/2306-1472.42.1814
2. Shushin N. A. Gas ejector with a tangential injection into the mixing chamber. Uchenye Zapiski TsAGI. 2010. V. XLI. No.3. Pp. 69-81. (in Russian).
https://doi.org/10.1615/TsAGISciJ.v41.i3.60
3. Sheveova H. M., Tynyna S. V. Ways of a two-phase flow control in the jet mill ejector channels. Geoteh. Meh. 2019. No. 144. Pp. 190-198. (in Russian).
https://doi.org/10.15407/geotm2019.144.190
4. Huang B., Chang J., Wang C., Petrenko V. A 1-D analysis of ejector performance. Int. J. Refrig. 1999. V. 22. No. 5. Pp. 354-364.
https://doi.org/10.1016/S0140-7007(99)00004-3
5. Kong F., Kim H. Analytical and computational studies on the performance of a two-stage ejector diffuser system. Int. J. Heat Mass Transf. 2015. V. 85. Pp. 71-87.
https://doi.org/10.1016/j.ijheatmasstransfer.2015.01.117
6. Gagan J., Smierciew K., Butrymowicz D., Karwacki J. Comparative study of turbulence models in application to gas ejectors. Int. J. Therm. Sci. 2014. V. 78. Pp. 9-15.
https://doi.org/10.1016/j.ijthermalsci.2013.11.009
7. Garc a del Valle J., Sierra-Pallares J., Garcia Carrascal P., Castro Ruiz F. An experimental and computational study of the flow pattern in a refrigerant ejector. Validation of turbulence models and real-gas effects. Appl. Therm. Eng. 2015. V. 89. Pp. 795-811.
https://doi.org/10.1016/j.applthermaleng.2015.06.064
8. Croquer S., Poncet S., Aidoun Z. Turbulence modeling of a single-phase R134a supersonic ejector. Part 1: Numerical benchmark. Int. J. Refrig. 2016. V. 61. Pp. 140-152.
https://doi.org/10.1016/j.ijrefrig.2015.07.030
9.Croquer S., Poncet S, Aidoun Z. Turbulence modeling of a single-phase R134a supersonic ejector. Part 2: Local flow structure and exergy analysis. Int. J. Refrig. 2016. V. 61. Pp. 153-165.
https://doi.org/10.1016/j.ijrefrig.2015.07.029
10.Mazzelli F., Little A.B., Garimella S., Bartosiewicz Y. Computational and experimental analysis of supersonic air ejector: Turbulence modeling and assessment of 3D effects. Int. J. Heat Fluid Flow. 2015. V. 56. Pp. 305-316.
https://doi.org/10.1016/j.ijheatfluidflow.2015.08.003
11. Besagni G., Inzoli F. Computational fluid-dynamics modeling of supersonic ejectors: screening of turbulence modeling approaches. Applied Thermal Engineering. 2017. V. 117. Pp. 122-144.
https://doi.org/10.1016/j.applthermaleng.2017.02.011
12. Menter F. R. Two-equation eddy-viscosity turbulence models for engineering application. AIAA Journal. 1994. V. 32. No. 8. Pp. 1598-1605.
https://doi.org/10.2514/3.12149
13. Fedorova N. N., Valger S. A., Danilov M. N., Zakharova Yu. V. Basics of Work in ANSYS 17. DMK Press, 2017. 210 pp. (in Russian).
14. Wilcox D.C. Turbulence Modeling for CFD. Griffin Printing, 1993. 460 pp.
15. Vallander S. V. Lectures on Hydroaeromechanics. Leningrad: Leningrad University, 1978. 312 pp. (in Russian).
16. ANSYS Fluent Theory Guide. Release 2019 R1. ANSYS, Inc. 2019. 922 pp.
Copyright (©) 2020 Ihnatev O. D., Shevelova H. M.
Copyright © 2014-2020 Technical mechanics
____________________________________________________________________________________________________________________________
|
GUIDE FOR AUTHORS
====================
Open Access Policy
====================
REGULATIONS
on the ethics of publications
====================
|