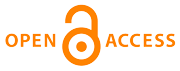 |
Home
>
Journal Issues
>
No 1 (2021) Technical mechanics
>
10
___________________________________________________
UDC 539.3
Technical mechanics, 2021, 1, 92 - 100
Experimental analysis of the mechanical characteristics of launch vehicle parts manufactured by FDM additive technologies
DOI:
https://doi.org/10.15407/itm2021.01.092
Derevianko I., Avramov K., Uspensky B., Salenko A.
Derevianko I.
Yuzhnoye State Design Office
Avramov K.
A. Pidgorny Institute of Mechanical Engineering Problems of the National Academy of Sciences of Ukraine
Uspensky B.
A. Pidgorny Institute of Mechanical Engineering Problems of the National Academy of Sciences of Ukraine
Salenko A.
National Technical University of Ukraine “Igor Sikorsky Kyiv Polytechnic Institute”
Additive manufacturing is very promising for aerospace engineering and aircraft construction. Using these
technologies, light structures with preset strength properties can be made. For lack of tables of the
mechanical properties of materials made by additive technologies, any calculation must be accompanied by
the experimental determination of their mechanical properties.
This paper presents an experimental approach to the determination of the mechanical characteristics of
parts printed by FDM technologies. Parts manufactured from polymers by FDM technologies are shown to be
orthotropic. Therefore, their elastic properties are described by nine constants: three Young’s moduli,
three shear moduli, and three Poisson ratios. A cube is printed for the experimental determination of
these constants. Six specimens are cut out from the cube. Three specimens are cut parallel to the cube
edges, and the other three are cut at an angle of 45° to them. Each such specimen is manufactured in
five pieces. This makes it possible to average the tensile stress–strain diagrams obtained for all the
components of the stress tensor. The mechanical properties of the material are determined from these
diagrams. The three Young’s moduli and the three Poisson ratios are determined from the three specimen
types parallel to the cube edges. The three shear moduli are determined from the specimens cut at an
angle of 45° to the cube edges. To determine these constants, tensile stress–strain diagrams are
obtained experimentally.
A technology is presented for manufacturing specimens on a Stratasys FORTUS 900 MC 3D printer. The
mechanical properties of two polymer materials (ULTEM 9085 and PLA) are determined and compared.
PLA has higher Young’s moduli and shear moduli and lower Poisson ratios than ULTEM 9085.
FDM technology, orthotropic polymer material, mechanical properties, 3D printer
1. Matthews N. Additive metal technologies for aerospace sustainment. Aircraft Sustainment and Repair. R. Jones, A. A. Baker, Neil Matthews, V. K. Champagne (Eds.). Elseveir, 2018. .Pp. 845-862
https://doi.org/10.1016/B978-0-08-100540-8.00015-7
2. Boparai K. S., Singh R. Advances in Fused Deposition Modeling. Reference Collection in Materials Science and Materials Engineering, Elseveier, 2017. Doi: 10.1016/B978-0-12-803581-8.04166-7.
https://doi.org/10.1016/B978-0-12-803581-8.04166-7
3. Byberg K. I., Gebisa A. W., Lemu H. G. Mechanical properties of ULTEM 9085 material processed by fused deposition modeling. Polymer Testing. 2018. V. 72. Pp. 335-347.
https://doi.org/10.1016/j.polymertesting.2018.10.040
4. Ahn S.-H., Montero M., Odell D., Roundy S., Wright P.K. Anisotropic materialproperties of fused deposition modeling ABS. Rapid Prototyping Journal. 2002. V. 8. No. 4. Pp. 248-257.
https://doi.org/10.1108/13552540210441166
5. Domingo-Espin M., Puigoriol-Forcada J.M., Garcia-Granada A.-A., Llumà J., Borros S., Reyes G. Mechanical property characterization and simulation of fused deposition modeling Polycarbonate parts. Materials & Design. 2015. V. 83. P. 670-677.
https://doi.org/10.1016/j.matdes.2015.06.074
6. Bellini A., Guceri S. Mechanical characterization of parts fabricated using fused deposition modeling. Rapid Prototyping Journal. 2003. V. 9. No. 4. Pp. 252-264.
https://doi.org/10.1108/13552540310489631
7. Casavola C., Cazzato A., Moramarco V., Pappalettere C. Orthotropic mechanical properties of fused deposition modelling parts described by classical laminate theory. Materials and Design. 2016. V. 90. Pp. 453-458.
https://doi.org/10.1016/j.matdes.2015.11.009
8. Chen Y., Li T., Jia Z., Scarpa F., Yao C.-W., Wang L. 3D printed hierarchical honeycombs with shape integrity under large compressive deformations. Materials and Design. 2018. V. 137. Pp. 226-234.
https://doi.org/10.1016/j.matdes.2017.10.028
9. Parsons E.M. Lightweight cellular metal composites with zero and tunable thermal expansion enabled by ultrasonic additive manufacturing: Modeling, manufacturing, and testing. Composite Structures. 2019. V. 223. Article 110656. DOI: 10.1016/j.compstruct.2019.02.031.
https://doi.org/10.1016/j.compstruct.2019.02.031
10. Gerisa A.W., Lenu H.G. Influence of 3D printing process parameters on tensile properties of ULTEM 9085. Procedia Manufacturing. 2019. V. 30. Pp. 331-338.
https://doi.org/10.1016/j.promfg.2019.02.047
11. Motaparti K. P., Taylor G., Leu M. C., Chandrashekhara K., Castle J., Matlack M. Effects of build parameters on compression properties for ULTEM 9085 parts by fused deposition modeling. Solid Freeform Fabrication. Proceedings of the 26th Annual International Solid Freeform Fabrication Symposium - An Additive Manufacturing Conference. 2016. Pp. 964-977.
12. Popescu D., Zapciu A., Amza C., Baciu F., Marinescu R. FDM process parameters influence over the mechanical properties of polymer specimens: A review. Polymer Testing. 2018. V. 69. Pp. 157-166.
https://doi.org/10.1016/j.polymertesting.2018.05.020
13. Zaldivar R.J., Witkin D.B., McLouth T., Patel D.N., Schmitt K., Nokes J.P. Influence of processing and orientation print effects on the mechanical and thermal behavior of 3D-printed ULTEM® 9085 material. Additive Manufacturing. 2017. V. 13. Pp. 71-80.
https://doi.org/10.1016/j.addma.2016.11.007
14. Chamis C.C., Sinclair J.H. Ten-deg off - axis test for shear properties in fiber composites. Experimental Mechanics. 1977. No. 17. Pp. 339-346.
https://doi.org/10.1007/BF02326320
15. ASTM D 3039. Standard Test Method for Tensile Properties of Polymer Matrix Composite. ASTM International. 2017. 13 pp.
16. Pagano N.J., Halpin J.C. Influence of end constraint in the testing of anisotropic bodies. Journal of Composite Materials. 1968. V. 2. No. 1. Pp. 18-31.
https://doi.org/10.1177/002199836800200102
17. Pierron F., Vautrin A. The 100 off-axis tensile test: a critical approach. Composites Science and Technology. 1996. V. 56. Pp. 483-488.
https://doi.org/10.1016/0266-3538(96)00004-8
18. Pindera M.J., Herakovich C.T. Shear characterization of unidirectional composites with the off-axis test. Experimental Mechanics. 1986. Pp. 103-112.
https://doi.org/10.1007/BF02319962
19. ASTM D3518. Standard Test Method for In-Plane Shear Response of Polymer Matrix Composite Materials by Tensile Test of a ±?45?^0 Laminate. ASTM International. 2018. 7 pp.
20. ASTM D638-14. Standard Test Method for Tensile Properties of Plastics. ASTM International. 2014. 17 pp.
21. ASTM D695-15. Standard Test Method for Compressive Properties of Rigid Plastics. ASTM International. 2015. 8 pp.
22. ASTM D790-17. Flexural properties of unreinforced and reinforced plastics and electrical insulating materials. ASTM International. 2017. 38 pp.
23. Carlsson L.A., Kardomateas G.A. Characterization of the mechanical properties of face sheet and core materials. Book: Structural and Failure Mechanics of Sandwich Composites, Solid Mechanics and its Applications. Springer, 2011. Pp. 19-37.
https://doi.org/10.1007/978-1-4020-3225-7_2
24. Avramov K. Bifurcations of parametric oscillations of beams with three equilibria. Acta Mechanica, 2003, V. 164. Pp. 115-138.
https://doi.org/10.1007/s00707-003-0022-9
Copyright (©) 2021 Derevianko I., Avramov K., Uspensky B., Salenko A.
Copyright © 2014-2021 Technical mechanics
____________________________________________________________________________________________________________________________
|
GUIDE FOR AUTHORS
====================
Open Access Policy
====================
REGULATIONS
on the ethics of publications
====================
|